Professional OEM Factory from China, focus on automotive tools and bearing puller,hand tools,Accepted customized and offer professional solution and appliactions for car mechanic and extractor bearings. Detail click nbdntools.com to learn more
Wednesday 29 December 2021
what is alloy steel? There are ofen display on tools introduced | DNT Auto Tools FAQ
Wednesday 22 December 2021
How To Change Your Oil by youself
Why change your own oil?
One of the cornerstones of do-it-yourself car maintenance jobs is the home oil change. It's a simple process that requires few tools, and it's a sure way to save some money while you avoid the hassle of sitting in a dull waiting room somewhere reading outdated magazines.
More than anything, the basic oil change is a great way to connect with your vehicle and take some control over its maintenance. The time you spend under the hood and under the car affords you an excellent opportunity to look around and see if anything else needs attention.
Money Saved: Between $25 and $75
Time Required: One hour the first time out; 30 minutes on average
Tools Required:
- Wrench to remove drain plug (box end or socket)
- Oil filter wrench
- Oil drain pan
- Funnel
- Latex gloves
- Jack and jack stands or ramps (optional, depends on ground clearance)
Materials Required:
- Oil
- Oil filter
- Replacement drain plug washer (depending on application)
Let's get started.
- Check the type and amount of oil needed
- Get together your filter, wrenches, and other supplies
- Prepare your vehicle
- Locate the oil filter and drain plug
- Drain the oil
- Tighten the drain plug
- Change the oil filter
- Add the new oil
- Check the oil level
Wednesday 15 December 2021
How to change automatic transmission fluid and filter | DNT Auto Tools FAQ
Wednesday 8 December 2021
Motorcycle Inner blind Bearing Puller Kit | DNT Auto Tools
- Heat Treated Steel, Open clamps by turning handle clockwise to snug against the bearing for pulling out evenly without damage the parts
- Connect with 1/2" 3/4" male thread water faucet.
Wednesday 1 December 2021
What is shock absorber and when to repair it and which professional tool will to select
A shock absorber is a mechanical part that sits beneath the wheel arches, and its role is to keep your tyres in permanent contact with the road so that you always have grip when you brake or turn a corner, and also ensures that you have a smooth, comfortable ride.
Why is it dangerous to drive with worn or damaged shock absorbers?
The average driver isn’t aware of the dangers of worn or broken shock absorbers, as they don’t see it or know about its function.Even worse, every time they drive themselves or others, they are at risk of an accident.
Here are the top ten dangers associated with worn/broken shock absorbers:
Reduced braking ability, which means longer stopping distances
ABS and ESP lose their efficiency
Increased risk of skidding on wet roads
Aquaplaning occurs at lower speeds
Less control in windy conditions or when caught in a crosswind
Increased driver tiredness
Increased wear and tear of tyres and other suspension parts
Uneven/oscillating headlight level dazzles on-coming drivers
Increased passenger discomfort
Increased risk of snaking when being towed
So,When you find your shock absorber is broken,Pls repair and replace them as soon as possible.
Wednesday 24 November 2021
How to Bearing puller maintenance and care | DNT Auto Tools FAQ
Wednesday 17 November 2021
How to Select a hydraulic system | DNT Auto Tools
Wednesday 10 November 2021
What's Different Types Of Pullers And The Key Features To Consider
Trying to remove shaft-mounted components without using the right types of puller can be frustrating and time-consuming. Interference fits, dirt, and corrosion can make the removal process difficult.
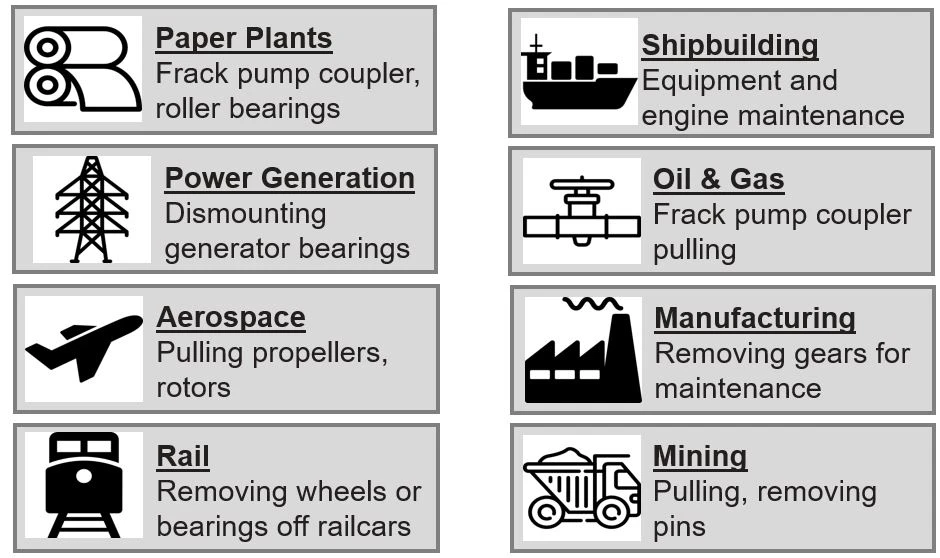
Wednesday 3 November 2021
How to find a right puller | DNT Auto Tools FAQ
Wednesday 27 October 2021
What's Different Types Of Pullers And The Key Features To Consider
Trying to remove shaft-mounted components without using the right types of puller can be frustrating and time-consuming. Interference fits, dirt, and corrosion can make the removal process difficult.
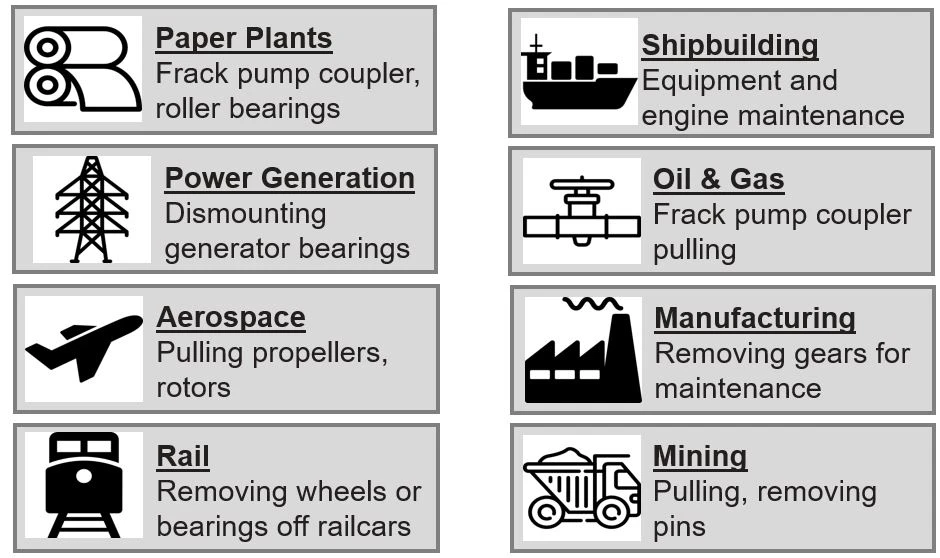
Wednesday 20 October 2021
How to find a right puller | DNT Auto Tools FAQ
Wednesday 13 October 2021
How To Test A Tool's Quality At The Hardware Store
How To Test A Tool's Quality at the Hardware Store | DNT Auto Tools FAQ:
Buying hand tools can be a confusing—and at times a losing—proposition. When faced with aisles full of putty knives, hammers, utility knives, and other toolbox must-haves, it’s tough to know if you’re really getting the best product for your money. If you’re like most people, you’ve probably purchased a few tools in the past that ended up breaking during use or rusting into a corroded mess soon after you brought them home, and you'd like to avoid that disappointing experience in the future.
Learn more follow 7 tips:
1. Look Up!
One of the simplest tricks for locating quality tools is to “look on the shelves above eye level,” Retail stores position mid-quality tools at eye level because those are the tools that most customers purchase—but they may not offer the best bang for your buck. With tools, as with many things in life, higher quality often comes at a slightly higher price. The superior materials and the manufacturing methods used to create better tools add a little to the final cost. Instead of grabbing the first putty knife you see, shift your focus upward. That’s where you’ll find higher-quality tools,
2. Feel the Weight
When shopping for a quality tool, “take it down off the shelf and feel the weight,” “A lightweight utility knife might be cheaper, but it might not feel as good in your hand.” Imagine using the tool: Is it substantial enough for you to grip firmly? Typically, a higher-quality tool will be little heavier than a substandard model.
There are exceptions, however. If a tool is used overhead—for example, when a wide taping knife is being used to smooth joint compound on ceilings—a heavy tool can be a burden. Consider how you will be using the tool, and then factor in whether it’s the best weight for your needs.
3. Look for Tools That Multitask
While higher-quality tools will often cost more, you can actually save money and still get top-notch durability and performance by choosing a tool that multitasks rather than buying many separate tools. “Additional benefits and features just make life easier,” A good example of a multitasking tool is the HYDE 5-in-1 Painter's Tool. This single tool opens paint cans, widens cracks for patching, doubles as a paint scraper or putty knife, and removes wet paint from a roller. Not only will you save money by buying a high-quality multipurpose tool instead of five (or more) individual tools to do the same work, you won’t have to lug around a lot of heavy tools in your tool belt—and you’ll get years of dependable service
4. Know Your Steel
A cheap, flexible tool is probably OK for a small or one-time job, but with repeated use, it can bend without resuming its original shape. Quality materials make for a quality tool. “Carbon steel is great for many hand tools,” “because it can be hardened to various degrees of rigidity, but there’s a problem—it rusts. The next step up, quality-wise, is stainless steel, which will cost more but won't pose the same issue.”Usually Alloy steel is better than carbon steel, high carbon steel is better than general steel
5. Consider Comfort
A tool with a poorly designed grip can leave you with aching muscles and tendons, or even blisters, if it doesn’t fit well in your hand. For repetitive-motion tasks, such as scraping paint from a fence or taping a room's worth of drywall joints, “look for a well-formed, cushioned grip that will absorb some of the motion or impact,”
Ergonomic handles and comfort grips allow you to complete your task without discomfort. Before buying, hold the tool in your hand as you would if you were using it. Does the handle feel good in your grasp? The bottom line: If a tool fits your hand comfortably, you’ll be able to work longer with less wrist and arm fatigue.
6. Look for Full Tang Construction
For example the knife, Perhaps the best indicator that a taping knife or putty knife will stand the test of time is full tang construction, which just means that “the metal in the blade goes all the way from the end of the handle to the tip of the blade,” “It’s one solid piece, so it will hold up better under pressure.”
Partial tang construction, on the other hand—which is often found in cheaper knives—features a tang that extends only a short way into the handle. After a few uses, a partial tang handle is likely to work loose, and then you’re stuck having to buy another knife to complete your project. Full tang knives last longer and offer increased leverage when performing tasks that require lateral pressure on the blade, such as prying a baseboard away from a wall. Sometimes, you can look at the handle of the knife from the side to see if the tang runs all the way to the end of the handle, though knives with overmold grips will fully encase the handle portion of the tang. If a knife is made with full tang construction, it should say so on the packaging.
7. Check Out the Warranty
When a manufacturer is confident that their product is top-notch, they’re more likely to offer a long-term or lifetime warranty against defects. Check the tool’s packaging for an indication that the manufacturer is offering a warranty.