Professional OEM Factory from China, focus on automotive tools and bearing puller,hand tools,Accepted customized and offer professional solution and appliactions for car mechanic and extractor bearings. Detail click nbdntools.com to learn more
Wednesday, 18 May 2022
New type of coil spring compressor tool set is out now! order quick | DNT Auto Tools News
Tuesday, 19 April 2022
What is a Wheel Hub Puller?How to remove wheel hub | DNT Auto Tools FAQ
Thursday, 7 April 2022
High quality oil filter wrench is out now!! welcome to send inquiry | DNT Auto Tools News
Wednesday, 30 March 2022
What is a puller set? | DNT Auto Tools FAQ
Wednesday, 23 March 2022
what's Drop Forging? DNT Tools' use Forging Techniques | DNT Auto Tools FAQ
Wednesday, 16 March 2022
Casting Process's Advantages/Disadvantages/Applications | DNT Auto Tools FAQ
Wednesday, 9 March 2022
What Is The Casting Process? | DNT Auto Tools FAQ
Wednesday, 2 March 2022
What is mechanical puller? | DNT Auto Tools FAQ
Wednesday, 23 February 2022
What Is a Gear Puller tool? | DNT Auto Tools FAQ
Wednesday, 16 February 2022
What are bearing pullers made of? | DNT Auto Tools FAQ
Chemical composition of 40Cr steel
rade | C | Si | Mn | Cr | Ni(≤) | Cu(≤) | P(≤) | S(≤) |
40Cr | 0.37-0.44 | 0.17-0.37 | 0.5-0.8 | 0.8-1.0 | 0.3 | 0.03 | 0.035 | 0.035 |
Sample blank size (mm):25
The first quenching heating temperature (ºC):850; coolant: Oil
Second quenching heating temperature (ºC):-
Tempering heating temperature (ºC):520;
Tensile strength (σb/MPa): ≥980
The yield point (σs/MPa): ≥785
Elongation (δ5/%): ≥9
Section shrinkage (ψ/%): ≥45
gear puller
40CR alloy steel is used to produce bearing pullers because it provides them with a very strong structure that is able to withstand wear.
Bearing pullers need to be able to remove bearings, gears or pulleys without becoming easily worn or damaged.
2. Heat Treated
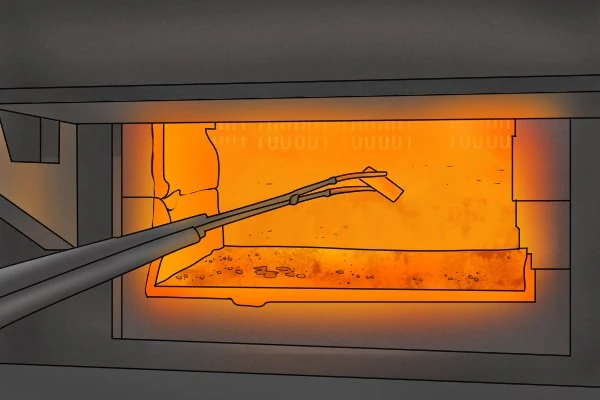
heat treated
Bearing pullers are heat treated for increased wear and strength.
3. Chrome plated
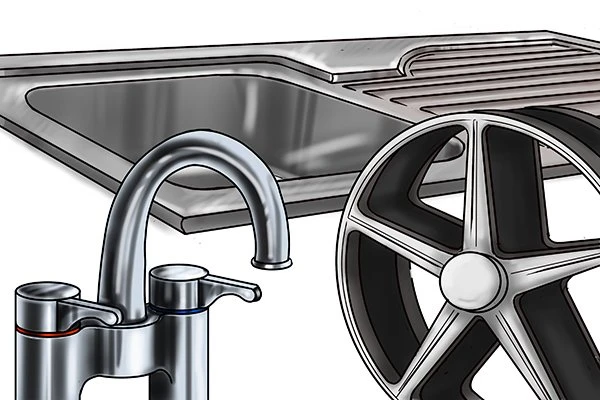
Chrome plated
The bearing pullers are chrome plated to resist corrosion. Corrosion is when iron reacts with oxygen and forms a reddish-brown oxide that we know as rust. When steel corrodes it deteriorates and eventually decays over time.
Wednesday, 9 February 2022
What are bearing pulllers | DNT Auto Tools FAQ
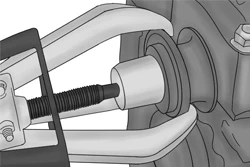
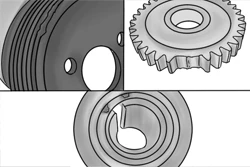
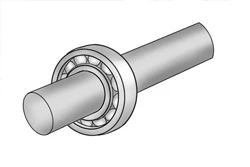
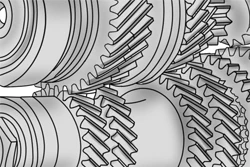
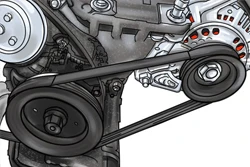
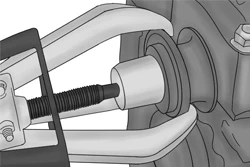
Wednesday, 19 January 2022
What bearing pullers sizes are available? | DNT Auto Tools FAQ
Thursday, 13 January 2022
Bearing Puller guide: choose right puller for your work | DNT Auto Tools FAQ
Wednesday, 5 January 2022
What's a Basic components of a hydraulic system | DNT Auto Tools FAQ
A hydraulic puller system needs 3 basic components to function:
Basic components of a hydraulic system
1.Puller
2. Hydraulic Cylinde
3. Pump (Air, hand, self-contained or electric)
The basic operation of a hydraulic puller system makes use of a cylinder that is fitted into the body of the puller. The cylinder replaces the center bolt function of a manual puller.
The technician inspects the component to be removed and selects the proper size puller. Safety precautions are taken in into consideration as the technician secures the jaws of the puller on the application to keep the system in place.
Instead of using a wrench to move the center bolt forward and backward as one would with a manual puller, a pump is used as a power source. The pump regulates the flow of hydraulic fluid.
As the hydraulic fluid pressure builds up, the pressure moves the cylinder forward pushing the ram of the puller to make contact with the shaft of the component being removed.